US Scientists Achieve Coal-Free Ironmaking: Cleaner Steel at Lower Costs?
Iron constitutes the foundation of contemporary society, utilized in structures ranging from skyscrapers and overpasses to vehicles and household devices.
In contrast, steel production stands as one of the globe’s biggest contributors to carbon emissions, largely because of the conventional method involving the extraction of iron from ore through coal-powered blast furnaces.
With the worldwide need for steel increasing steadily, developing environmentally friendlier and more sustainable ways to produce it becomes essential—not only for meeting our climate targets but also for the sustainability of industries globally.
Currently, scientists are exploring electrochemistry as a new approach to produce iron, which is essential for making steel.
Rather than depending on high-temperature, fossil fuel-powered furnaces, this innovative technique employs electricity to obtain pure iron from iron oxide at considerably cooler temperatures and with dramatically reduced emissions.
This represents a hopeful move towards a more environmentally friendly steel sector—a development that might aid in reducing emissions without compromising quality or financial gains.
Reevaluating iron ore for large-scale industry
At the University of Oregon, chemist Paul Kempler and his group are working on an electrochemical method that converts iron oxide and seawater into pure iron metal, simultaneously yielding chlorine, which has significant commercial value as a byproduct.
This technique has the potential to dramatically reduce the environmental footprint of conventional iron production and may ultimately become as affordable as current carbon-intensive methods.
The team demonstrated last year that electrochemistry can effectively transform iron oxide into iron in laboratory conditions.
However, actual iron ores found in nature are much more complicated than the refined substances utilized in previous experiments.
To make their process more applicable for industry, the researchers had to determine which kinds of natural iron oxides would be most effective in these lower-temperature reactions.
"We have a fundamental chemistry principle, essentially a guiding design rule, that can instruct us on identifying inexpensive iron oxides suitable for use in these reactors," Kempler stated.
Shape over size!
To address this query, postdoctoral researcher Ana Konovalova and graduate student Andrew Goldman explored how the form and architecture of iron oxide particles influence the procedure.
They developed particles that were both porous and dense, featuring comparable compositions yet distinct internal structures.
The results they found were straightforward: porosity plays a crucial role. Particles with greater porosity, possessing an increased internal surface area, facilitated quicker and more efficient production of iron.
Thick particles, conversely, decelerated the process and restricted the amount of iron that could be produced simultaneously.
“Thanks to the highly permeable particles, we can produce iron very rapidly over a compact space,” Goldman stated. “Dense particles aren’t capable of matching this speed, which restricts our ability to generate more iron per square meter of electrodes.”
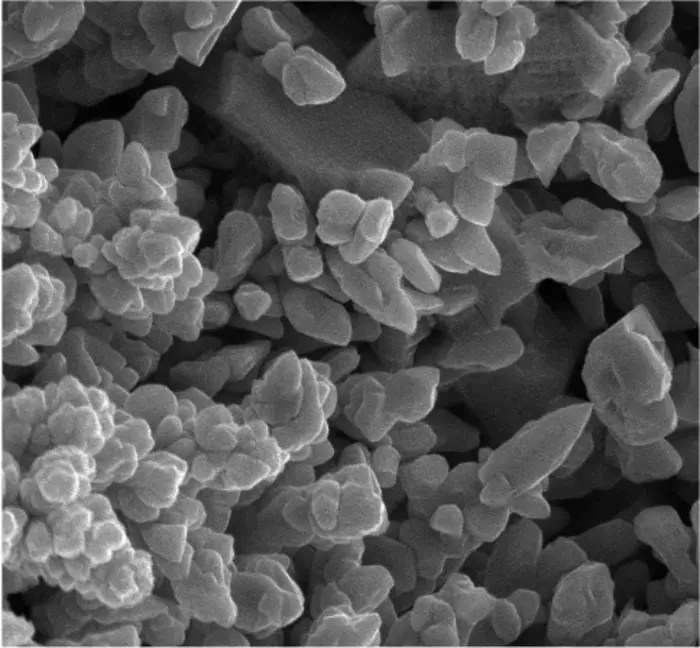
A big leap forward
Efficiency goes beyond a scientific achievement; it's essential for business survival. Given that large-scale electrochemical facilities come with significant costs, the quicker a system can generate iron, the faster it will recoup its investment.
Utilizing porous particles, the group projected they might create iron For less than $600 per metric ton, this is comparable to traditional ironmaking methods.
Future improvements in electrode design and porous material substrates might enhance the process even more.
To speed up the journey from laboratory to industry, the team is working alongside civil engineers at Oregon State University as well as an electrode production firm.
"I believe this research demonstrates that technology has the potential to fulfill the demands of an industrial society without causing significant environmental harm," Goldman stated.
We haven't resolved all the issues. problems Still, of course, but I believe it acts as an example that becomes a starting point for contemplating solutions from a new perspective."
The study appears in ACS Energy Letters .
Posting Komentar untuk "US Scientists Achieve Coal-Free Ironmaking: Cleaner Steel at Lower Costs?"
Please Leave a wise comment, Thank you